罗拉牵伸的基本原理:
一.牵伸概述 (一)实现牵伸的条件 在纺纱过程中,将须条抽长拉细的过程称为牵伸(drafting)。须条的抽长拉细是须条中纤维沿长度方向作相对运动的结果,所以牵伸的实质是纤维沿须条轴向的相对运动,其目的是抽长拉细须条到达规定的线密度。在牵伸过程中由于纤维的相对运动,使纤维得以平行、伸直,在一定条件下,也可以使产品中的纤维束分离为单纤维。 并条机的牵伸机构由罗拉和皮辊组成牵伸钳口。每两对相邻的罗拉组成一个牵伸区,在每个牵伸区内实现牵伸的条件是: (1) (1) 每对罗拉组成一个有一定握持力的握持钳口。 (2) (2) 两个钳口之间要有一定的握持距,这个距离稍大于纤维的品质长度,以利于牵伸的顺利进行,并可以避免损伤纤维。 (3) (3) 两对罗拉钳口之间应有速度差,即前一对罗拉的线速度应大于后一对罗拉的线速度。 (二)机械牵伸与实际牵伸 须条被抽长拉细的倍数称为牵伸倍数。用牵伸倍数可以表示牵伸的程度。如图5-3-1所示为牵伸作用示意图。
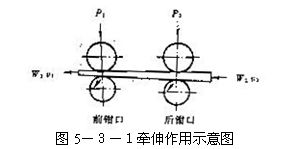
设各对罗拉之间不产生滑移,则牵伸倍数E可以用下式表示: E=V1/V2 (5-3-1) 式中;V1―――――表示罗拉输出速度; V2―――――表示罗拉喂入速度。 假设在牵伸过程中无纤维散失,则单位时间内自牵伸区中输出的产品质量与喂入的产品质量应相等, 即V1×W1=V2×W2 ,E=V1/V2=W2/W1 (5-3-2) 式中:W1―输出产品单位长度的质量; W2―喂入产品单位长度的质量。 实际上,牵伸过程中有落棉产生,皮辊也有滑溜现象,前者使牵伸倍数增大,后者使牵伸倍数减小,因而,不考虑落棉与皮辊滑溜的影响,用输出、喂入罗拉线速度求得的牵伸倍数,称为机械牵伸倍数或计算牵伸倍数;考虑了上述因素求得的牵伸倍数称为实际牵伸倍数。 实际牵伸倍数可以用牵伸前后须条的线密度或定量之比求得。 E/ =Tt2/Tt1=W2//W1/ (5-3-3) 式中:E/―实际牵伸倍数; W1/―输出产品的定量; W2/―喂入产品的定量; Tt1―输出产品的线密度; Tt2―喂入产品的线密度。 实际牵伸倍数与机械牵伸倍数之比称为牵伸效率η。即: η=E//E×100% (5-3-4) 在纺纱过程中,牵伸效率常小于1,为了补偿牵伸效率,生产上常使用的一个经验数值是牵伸配合率,它相当于牵伸倍数的倒数1/η。为了控制纺出纱条的定量,降低重量不匀率,生产上根据同类机台,同类产品长期实践积累,找出牵伸效率变化规律,然后在工艺设计中,预先考虑牵伸配合率,由实际牵伸与牵伸配合率算出机械牵伸,从而确定牵伸变换齿轮,即能纺出符合规定的须条。 (三)总牵伸倍数与部分牵伸倍数 一个牵伸装置,常由几对牵伸罗拉组成,从最后一对喂入罗拉至最前一对输出罗拉间的牵伸倍数称为总牵伸倍数;其相邻两对罗拉间的牵伸倍数称为部分牵伸倍数。 设由四对牵伸罗拉组成三个牵伸区,罗拉线速度自后向前逐渐加快,即V1>V2>V3>V4 ,各部分牵伸倍数分别是:E1=v1/v2;E2=v2/v3;E3=v3/v4 。 总牵伸倍数:E=v1/v4 。 将三个部分牵伸倍数连乘,则 E1×E2×E3=(v1/v2)×(v2/v3)×(v3/v4)=v1/v4=E (5-3-5) 即总牵伸倍数等于各部分牵伸倍数的乘积。 二。伸区内的纤维运动 牵伸的基本作用是使须条中纤维与纤维之间产生相对移动,使纤维与纤维头端之间的距离拉大,将纤维分布到较长的片段上。假设两根纤维牵伸之前头端之间距离为a ,牵伸之后纤维头端距离加大使纤维头端距离产生变化,这种变化称为移距变化。 经过牵伸后,产品的长片段不匀有很大的改善,其条干不匀(短片段不匀)却增加了,这说明牵伸对条干均匀度起着不良影响。为此,我们从研究牵伸过程中纤维的运动规律及牵伸前后纤维移距变化着手,掌握牵伸过程中纤维的运动规律,从而控制条干均匀度。 (一)牵伸后纤维的正常移距 如图5-3-2 所示是两对罗拉组成的牵伸区。假设A、B是牵伸区内两根等长且平行伸直的纤维,牵伸之前A、B头端距离为a0,假设两根纤维都在同一变速点(前钳口线处)变速。变速之前两根纤维都以后罗拉表面速度v1前进,由于纤维A头端在前,到达变速点的时间较早,变速后以前罗拉速度v2前进。纤维A变速后,纤维B仍以较慢的速度v1前进直到前钳口线。 假设纤维B到达前钳口线所需时间为t,则t=a0/v1; 在同一时间内纤维A所走的距离为a1,且 a1=v2×t=v2×(a0/v1)=(v2/v1)a0=Ea0 (5-3-6) 即经过牵伸后,两根纤维A、B之间的头端距离增大了E倍。假若纱条截面内所有纤维 在同一变速点变速经过牵伸后,各根纤维头端距离均扩大为原来的E倍,这样,牵伸前后纱条条干均匀度没有变化。我们把这种移距变化即a1=Ea0称为正常移距。
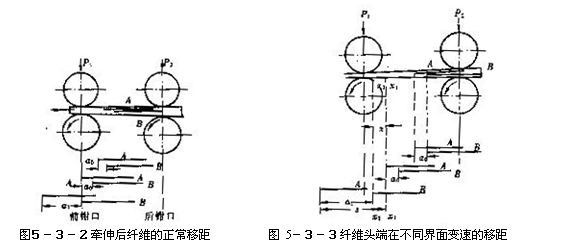
(二)移距偏差 通过对纤维进行移距试验,即用两根不同颜色的纤维夹在须条中,牵伸前其头端距离为a0 ,则经过E倍牵伸后,在输出的须条中测量这两根纤维的头端距离为a1。在反复试验中发现a1有时大于Ea0,而有时小于Ea0,很少等于Ea0,这说明在实际牵伸中纤维头端并不在同一截面上变速,从而使牵伸后须条条干均匀度恶化。 如图5-3-3所示。设纤维A在x1-x1界面上变速,而纤维B到达x2-x2界面上才变速(即头端在前的纤维先变速,头端在后的纤维后变速),纤维A变速后以较快的速度v2运动,而纤维B仍以v1运动。 当纤维B到达变速界面x2-x2时所需时间为t=(a0+x)/v1; 在同一时间内纤维A所走的位移为 a1+x=t×v2=[(a0+x)/v1]×v2=E(a0+x) a1=E(a0+x)-x=Ea0+(E-1)x (5-3-7) 由上式可知,由于前面纤维变速较早,后面纤维变速较晚,使牵伸后纤维头端距离较正常移距偏大。 同理,假设纤维A在x2-x2界面上变速,而纤维B在x1-x1界面上变速,即头端在前的纤维变速点在后,头端在后的纤维变速点在前,且a0>x,则当纤维A在x2-x2界面上变速后,纤维B尚须以速度v1移动一段距离(a0-x)才到达x1-x1界面而变速,所需时间为 t=(a0-x)/v1 在同一时间内,纤维A移动的距离为a1-x,则 a1-x=v2t=v2(a0-x)/v1=E(a0-x) a1=E(a0-x)+x=Ea0-(E-1)x (5-3-8) 上式说明由于前面纤维变速较晚,后面纤维提前变速,牵伸后纤维的移距较正常移距为小。 综合上述两种情况,两根纤维在不同截面上变速后,头端的移距为 a1=Ea0±(E-1)x (5-3-9) 式中Ea0为须条经E倍牵伸后纤维头端的正常移距,(E-1)x为牵伸过程中纤维头端在不同界面上变速而引起的移距偏差。由此可见,在实际牵伸过程中,正是由于纤维头端不在同一位置变速,而引起的移距偏差,使须条经牵伸后产生附加不匀。在牵伸区内,若棉条的某一截面上有较多的纤维变速较早,使纤维头端距离较正常移距为小,便产生粗节,在粗节后面紧跟着的就是细节;反之,若有较多的纤维变速较晚,便产生细节,在细节之后紧跟着的就是粗节。从移距偏差(E-1)x可知,当纤维变速位置越分散(x值越大),牵伸倍数E越大时,则移距偏差越大,条干越不均匀。因此,在牵伸过程中,使纤维变速位置尽可能向前钳口集中,即x→0,是改善条干均匀度,提高牵伸能力的重要条件。 (三)纤维变速点的分布 为了研究牵伸过程中纤维的变速界面,可采用以下方法进行试验测试。 如图5-3-4所示,在牵伸装置内放好试验用的棉条,在开车前将数根染有不同颜色的纤维头端,按等距离依次夹在棉条内,并在棉条上做一记号O(扎结一根色纱),量出记号O和最末一根染色纤维的头端距离bi,如图甲;然后开车,使染色纤维进入牵伸区,当最后一根染色纤维到达变速界面前,该纤维仍以后罗拉速度运动,其头端到记号O的距离bi不变,如图乙,直到这根纤维从前罗拉输出,而记号O尚未进入牵伸区立即停车,如图丙。测量记号O至前钳口线的距离s,前钳口线至染色纤维头端距离ci,即可计算出纤维头端变速点与前钳口线的距离xi。
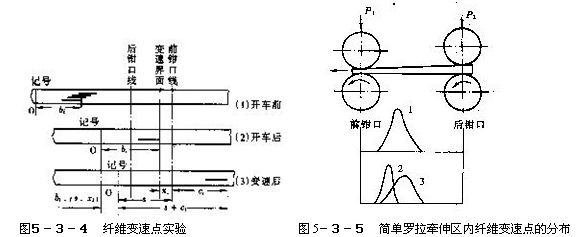
由于纤维在距前钳口线xi处变速,从变速点开始到关车的过程以速度v1走过(xi+ci)的距离,在此段时间内,记号O以速度v2走过的距离为bi-(s-xi)=bi+xi-s。 则 (xi+ci)/v1=(bi+xi-s)/v2 xi=[ci-E×(bi-s)]/(E-1) (5-3-10) 因此,根据各根染色纤维的bi及ci值,便可算出各根染色纤维的变速点与前钳口线间的距离 xi值。 根据试验,简单罗拉牵伸区内纤维变速点分布如图5-3-5 所示。 图中纵坐标表示纤维数量。 试验表明:(1)在牵伸过程中,纤维头端的变速界面xi(变速点至前钳口距离)有大有小,各个变速界面上变速纤维的数量也不相等,因而形成一种分布,即为纤维变速点分布(曲线1)。 (2)同样长度的纤维其头端也不在同一位置变速,同样呈现一种分布,长纤维变速点分布较集中且向前钳口靠近(曲线2);短纤维变速点分布较分散且距前钳口较远(曲线3)。 (3)在牵伸倍数一定的条件下,随着牵伸区隔距的增大,则变速点分布的离散性增加,变速点距前钳口的距离愈远;在隔距相同的条件下,随着牵伸倍数的增加,则变速点分布的离散性越小,且变速点位置靠近前钳口。 (4)为了获得均匀的产品应使纤维头端变速点分布尽可能向前钳口处集中而稳定。 实际上纤维变速点分布是不稳定的,即各变速界面变速纤维的数量是变化的。当变速点分布曲线向前钳口偏移,说明有比较多的纤维推迟变速,牵伸后输出的产品必然出现细节;当变速点分布曲线向后偏移,说明比较多的纤维提前变速,牵伸后输出的产品必然出现粗节。因此,变速点分布不稳定,是产品条干恶化的主要原因。在牵伸过程中,使纤维变速点分布集中而稳定,是保证产品条干均匀的必要条件。 三.牵伸区内纤维数量的分布 在牵伸区内,由后钳口向前钳口方向,从出现快速纤维开始,须条截面中的纤维数量即开始变化。愈向前,快速纤维越多,须条截面中纤维数量越少,在前钳口,所有的纤维均变为快速纤维,结果从后钳口到前钳口的须条截面内的纤维数量由多变少形成一种分布。如图5-3-6所示。 钳口间的须条可用切段称重法得到各截面的纤维数量分布曲线N(x)。后钳口内的纤维数量等于喂入须条横截面内平均纤维根数N2,前钳口的纤维数量等于输出须条横截面内的平均纤维根数N1,且N2/N1=E 。在设法除去牵伸区中的浮游纤维后(用夹持梳理法),即可得到前后钳口握持的纤维(简称前纤维或后纤维);再用切段称重法得到前钳口握持的纤维数量分布曲线N1(x)和后钳口握持的纤维数量分布曲线N2(x)。 如果以N(x)曲线为基准,将快速纤维数量分布曲线N1(x)离底线的垂直距离相应地移至N(x)曲线下,这样图乙中的上部和下部阴影部分分别为前纤维和后纤维在牵伸区内的数量分布,介于两者之间的空白部分,表示既不被前钳口握持又不被后钳口握持的那部分纤维即浮游纤维的数量分布。 通常牵伸区内,在罗拉握持可靠的条件下,前纤维为快速纤维,后纤维为慢速纤维,而浮游纤维受其周围快速纤维和慢速纤维影响速度不稳定。一般在后钳口处,由于其周围纤维多为慢速纤维,所以浮游纤维为慢速纤维;在前钳口处,由于其周围多为快速纤维,且越向前快速纤维数量越多,所以,浮游纤维变为快速纤维。按前、后纤维的比例,把浮游纤维分配成快速纤维和慢速纤维两部分,再和前后纤维相加,得到快速纤维的数量分布k(x)和慢速纤维的数量分布K(x)。
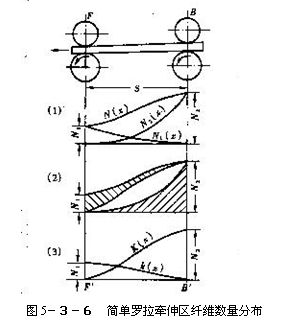
四.牵伸区内须条摩擦力界及其分布 纤维在牵伸过程中的运动决定于牵伸过程中作用于纤维上的外力。作用在整个须条中各根纤维上的力如果不均匀、不稳定,就会引起纤维变速点的分布不稳定。 (一)罗拉钳口的摩擦力界分布 在牵伸区中,纤维与纤维间、纤维与牵伸装置部件之间的摩擦力所作用的空间称为摩擦力界。摩擦力界具有一定的长度、宽度和强度。牵伸区中,纤维之间各个不同位置摩擦力强度不同所形成的一种分布,称为摩擦力界分布。摩擦力界每一点上摩擦力的大小,主要决定于纤维间压应力的大小,所以纤维间压应力的分布曲线,在一定程度上可以近似地代表摩擦力界的分布曲线。如图5-3-7中(1),表示一对罗拉作用下须条轴线方向摩擦力界分布情况。
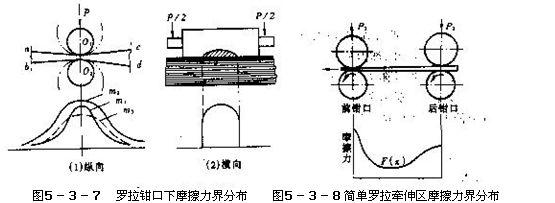
由于上罗拉垂直压力P的作用,须条被上下罗拉握持,因而使纤维间产生压应力。这个应力的分布区域不仅作用在通过上下罗拉轴线的垂直平面上,而且还扩展到这个平面两侧的空间,在上下罗拉轴线的垂直平面O1O2上压应力最大,纤维接触最紧密,纤维间产生的摩擦力强度也最大,摩擦力界分布曲线在这个位置是峰值。在O1O2两侧,压应力逐渐减小,摩擦力强度也逐渐减小,形成一种中间高两端低的分布。当皮辊加压、罗拉直径、棉条的定量变化时,其摩擦力界的分布也会变化,其规律如下: 1.皮辊加压 皮辊的压力增加,钳口内的纤维丛被压得更紧,摩擦力界长度扩展,且摩擦力界强度分布得峰值也增大(曲线m2)。 2.罗拉直径 罗拉直径增大时,摩擦力界纵向长度扩展,但摩擦力界峰值减小。这是因为同样的压力分配在较大的面积上(曲线m3)。 3.棉条定量 棉条定量增加,而其他条件不变,则加压后须条的宽度与厚度均有所增加,加大了与皮辊和罗拉的接触面积,摩擦力界分布曲线的峰值降低,长度扩展,与m3形态相似。 图5-3-7中(2)是沿须条横截面方向的罗拉钳口下的摩擦力界分布,这个方向的分布简称横向分布。当皮辊加压后,由于皮辊富有弹性和变形,须条完全被包围,中部的须条压缩得紧密,摩擦力界强度最大,两侧的须条,由于皮辊的变形,也受到较大的压力,所以,横向摩擦力界的分布比较均匀。 牵伸过程中,对纤维运动的控制是否完善,与摩擦力界的纵向分布密切相关,至于横向摩擦力界,只要求做到适当地约束须条,使之不过于向两侧扩散,保持须条横向分布均匀,摩擦力界分布均匀即可。 在一个牵伸区中,两对罗拉各自形成的摩擦力界连贯起来,就组成了简单罗拉牵伸区中整个摩擦力界分布。如图5-3-8 所示。可见,中部摩擦力界的强度较弱,所保持的只是纤维间的抱合力,因而控制纤维的能力较差,致使较短的纤维变速点不稳定,恶化产品条干。可采用紧隔距、重加压增强中部摩擦力界。 五.引导力和控制力 牵伸区内任意一根浮游纤维都被周围的快速纤维和慢速纤维所包围。快速纤维作用于浮游纤维上的摩擦力fa称为引导力。慢速纤维作用于浮游纤维上的力fv称为控制力。控制力使浮游纤维保持慢速,而引导力则使浮游纤维快速前进。一根浮游纤维在牵伸区内所处不同位置时,作用于其上的引导力和控制力也不相同。当引导力大于控制力时,就能使浮游纤维变速。 如图5-3-9所示,牵伸区内任意一根长度为lf的浮游纤维,其头端位于x1位置时,尾端位于(x1-lf)的位置,它被周围的快速纤维l1和慢速纤维l0所包围。
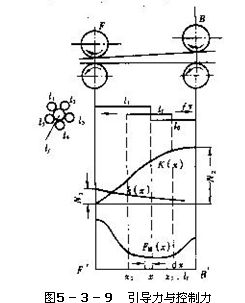
由于牵伸区内纵向摩擦力界强度分布为FM(x),在任一截面x上,浮游纤维lf的微小片段dx受到周围纤维的摩擦力总和为FM(x)dx;由于牵伸区内快慢纤维的数量分布,慢速纤维对浮游纤维lf的接触机率为K(x)/[k(x)+K(x)],快速纤维对它的接触机率为k(x)/[k(x)+K(x)]。则快速纤维对浮游纤维的引导力为:
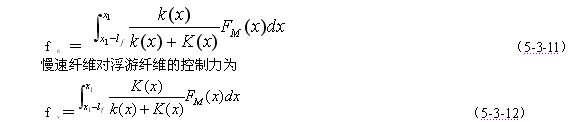
显然,当fa>fv时,该纤维改为快速运动;当fa<fv时,该纤维仍保持原来慢速运动。 影响引导力和控制力的主要因素有:接触的快、慢速纤维的数量;摩擦力界的强度分布;浮游纤维本身的长度和处在须条中的位置,以及纤维的摩擦性能。 为了使牵伸过程中浮游纤维运动保持稳定,必须使引导力和控制力稳定。 六.牵伸力和握持力 牵伸区中,前钳口所握持的须条是由快速纤维组成,后钳口所握持的须条是由慢速纤维所组成。罗拉钳口必须具有足够的握持力来克服所有快速纤维和慢速纤维间的摩擦力,牵伸作用才能顺利进行。 (一) (一) 牵伸力和握持力 1.牵伸力 牵伸过程中,以前罗拉速度运动的快速纤维从周围的慢速纤维中抽出时,所受到的摩擦阻力的总和,称为牵伸力。 牵伸力与控制力、引导力是有区别的,牵伸力是指须条在牵伸过程中受到的摩擦阻力,而控制力和引导力是对一根纤维而言的。牵伸力与快、慢速纤维的数量分布及工艺参数有关。 由于任意一根纤维受到周围的慢速纤维的摩擦阻力称为控制力,故牵伸力T可以从控制力的概念由公式(5-3-12)导出:

式中lm:纤维最大长度。S:前后钳口间的距离。 2.握持力 在罗拉牵伸中,为了能使牵伸顺利进行,罗拉钳口对须条要有足够的握持力,以克服须条牵伸时的牵伸力。所谓罗拉握持力是指罗拉钳口对须条的摩擦力。其大小取决于钳口对须条的压力及上下罗拉与须条间摩擦系数。如果罗拉握持力不足以克服须条上的牵伸力时须条就不能正确地按罗拉表面速度运动,而在罗拉钳口下打滑,造成牵伸效率低,输出须条不匀,甚至出现“硬头”等不良后果。
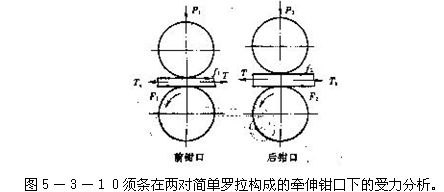
在前钳口,前罗拉作用于须条的摩擦力F1与须条的运动方向相同,皮辊对须条的摩擦力f1与须条的运动方向相反,而牵伸力T是快速纤维受到慢速纤维的摩擦力的总和,故T与须条的运动方向相反。因而正常牵伸时,为了防止须条在钳口下打滑,前钳口握持须条的条件是: F1-f1≥T (5-3-14) 后钳口握持的须条,在牵伸力T的作用下,有向前滑动的趋势,故T与须条的运动方向相同,而后罗拉作用于须条的摩擦力F2及后皮辊作用于须条的摩擦力f2都与须条的运动方向相反。因而,正常牵伸时,后钳口握持须条的条件是: F2+f2≥T (5-3-15) 由以上分析可知,前后钳口的实际握持力分别为(F1-f1)及(F2+f2)。因此欲使前后钳口同样达到与牵伸力相适应的握持力,则F1>F2,故前皮辊上的压力P1应大于后皮辊上的压力P2。 (二) (二) 影响握持力和牵伸力的因素 1.影响握持力的因素 握持力的大小决定于上下罗拉与须条的摩擦系数及罗拉上的加压。因此,影响握持力的因素,除罗拉加压外,主要有皮辊的硬度,罗拉表面沟槽的形态及槽数,同时由于皮辊磨损中凹,皮辊芯子缺油而回转不灵活,罗拉沟槽棱角磨光等,对握持力亦有很大影响。牵伸装置对各对罗拉上所加压力的大小是通过实验确定的。一般应使钳口的握持力比最大牵伸力大2~3倍。 2.影响牵伸力的因素 影响牵伸力的因素很多,主要有以下几个方面: (1) (1) 牵伸倍数: ① ① 当喂入棉条的线密度一定时,牵伸倍数与牵伸力的关系如图5-3-11所示。当牵伸倍数等于1时,纤维间没有相对滑移,牵伸力为零;此后,随着牵伸倍数的提高,须条呈张紧状态,牵伸力随牵伸倍数的增大而急速增大;在牵伸倍数接近临界值Ec时,纤维间开始产生滑动,当牵伸倍数超过Ec后,钳口下纤维数量减少,牵伸力下降。实验表明,棉条临界牵伸倍数Ec=1.2~1.3。 ② ② 当输出棉条线密度维持不变,喂入棉条的线密度增大。牵伸倍数增大,此时虽然前纤维数量不变,但由于后纤维数量增加,后钳口摩擦力界向前扩展,因而使每根纤维所受到的阻力增加,牵伸力也随之增加。因此,牵伸力随着牵伸倍数的增大而增大。 等不良后果。
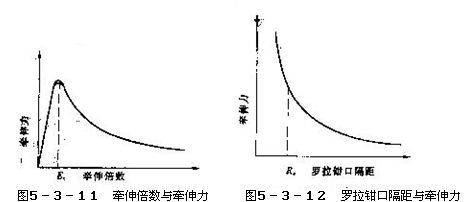
(2)罗拉握持距 当罗拉隔距变化时,牵伸力的变化曲线如图5-3-12所示,罗拉隔距增大,牵伸力减小,但到一定程度后隔距再增大时,牵伸力几乎没有变化,因为此时快速纤维的后端受到摩擦力界的影响较小。反之,当罗拉隔距缩小到一定程度后,快速纤维尾端受到后罗拉摩擦力界的影响较大,部分长纤维可能同时受到前后罗拉的控制,牵伸力剧增,使纤维拉断或牵伸不开而出现“硬头”。 (3)皮辊加压 牵伸区中后钳口皮辊压力增大,后摩擦力界强度、范围增大,牵伸力也随之增大。 (4)附加摩擦力界 由于曲线牵伸机构的后摩擦力界扩展,因此,即使后钳口处压力与简单罗拉牵伸相同,牵伸力也较大。如牵伸机构中采用集合器,压力棒等都会使牵伸区内附加摩擦力界增大,牵伸力增大。 (5)喂入棉条的厚度和密度 当喂入棉条厚度增大时,摩擦力界分布长度扩展,牵伸力变大。实验证明,当其他条件不变时,两根棉条并列喂入,其牵伸力为单根棉条的两倍;两根棉条上下重叠喂入,牵伸力为单根棉条的3.2倍。 (6)纤维性质等的影响 纤维长度长,细度细,则同样号数的须条的截面中纤维根数多,且纤维在较大的长度上受到摩擦阻力,所以牵伸力大,同时接触的纤维数量较多,抱合力一般较大,因而增加了牵伸力。此外,纤维的平行伸直度愈差,纤维相互交叉纠缠摩擦力较大,牵伸力增大。 (7)温湿度 温湿度与牵伸力密切相关。温度增高时,纤维间摩擦系数小,牵伸力降低。一般情况下,相对湿度增大,纤维摩擦系数增加,但相对湿度在34%~76%时,相对湿度增加,牵伸过程中纤维易于平行伸直,牵伸力反而降低。 (三)对牵伸力和握持力的要求 牵伸力反映了牵伸区中快速纤维与慢速纤维之间的联系力,由于这种联系力的作用,使得须条紧张,并引导慢速纤维在紧张伸直的状态下转变速度。因此,牵伸力应具有一适当的数值,并保持稳定,这是保证牵伸区纤维运动稳定的必要条件。牵伸力不应过大,因为过大就意味着快速纤维与慢速纤维之间联系力非常紧密,易带动慢速纤维提前变速,而使变速点分布离散度增加,恶化须条条干。 同时,如果前罗拉钳口对纤维的握持力小于牵伸力,会引起须条在钳口下打滑,牵伸不开。 握持力必须大于牵伸力,才能使牵伸正常进行,一般握持力应比牵伸力大2~3倍。 七.牵伸区内纤维运动的控制 在牵伸过程中,控制纤维的运动,是提高须条均匀度的关键。 牵伸装置对纤维运动的控制是依靠其对须条的摩擦力界合理布置而建立的。 1.摩擦力界布置 摩擦力界布置应该使其一方面满足作用于个别纤维上的要求,同时又能满足作用于整个牵伸须条上力的要求。 对于个别纤维而言,适当加强控制力,并减少引导力,可以使纤维变速点向前钳口靠近,并有利于变速点的相对稳定。 对于整个须条而言,牵伸力应具有适当数值,并保持稳定。根据适当加强对浮游纤维的控制力,并减弱其对引导力的要求,在牵伸区纵向,应将后钳口的摩擦力界向前逐渐扩展并逐渐减弱,意味着加强慢速纤维对浮游纤维的控制,同时又能让比例逐渐增加的快速纤维从须条中顺利抽出,而不影响其他纤维的运动。 前钳口摩擦力界在纵向分布状态应高而狭,以便稳定地发挥对浮游纤维的引导作用,这样,可以保证纤维变速点分布向前钳口附近集中且相对稳定。 2.附加摩擦力界的应用 根据摩擦力界分布的理论要求,仅有二对罗拉组成的摩擦力界分布是不能满足要求的。在牵伸区域中,由于二对罗拉之间有一定的隔距,且隔距主要适应所加工纤维长度的需要,因此由两对罗拉所建立的摩擦力界,其扩展到牵伸区的中部时,强度已经很弱,甚至在牵伸区中部的较长一段距离上,摩擦力界主要依靠纤维之间的抱合力来建立,因此控制力和引导力不稳定,波动较大,在此情况下,浮游纤维的运动将不能得到很好的控制,变速点分布离散度大,且不稳定。因此,需要在牵伸区中装有附加摩擦力界,以加强牵伸区中部摩擦力界,达到既控制浮游纤维运动,又不阻碍快速纤维运动的作用。 目前,常用的附加摩擦力界机构为皮圈、轻质辊、压力棒、曲线牵伸等形式来增加中部摩擦力界,改善对纤维运动的控制。 八.纤维的伸直平行作用 通过牵伸可以提高须条中纤维的平行伸直度,改善须条中纤维的弯钩状态,提高成纱质量。 (一) (一) 平行伸直的概念 一根纤维在空间的真实长度(或称原始长度)为ab,如图5-3-13所示,向任意平面x-x/ 的最大投影长度为cd,则纤维的伸直度ξ及平行度p分别为: ξ=cd/ab×100% (5-3-16) p=cosθ=cd/a/b/×100% (5-3-17)
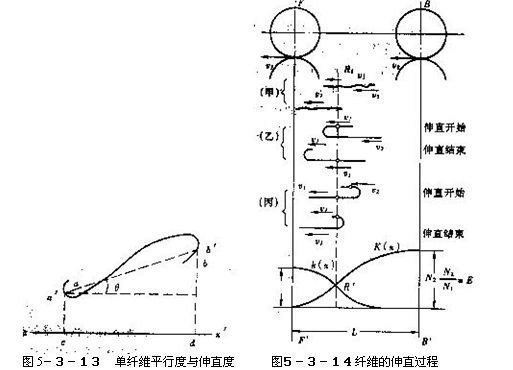
牵伸过程中纤维的伸直过程,就是纤维自身各部分间发生相对运动的过程。在须条中纤维的形态一般分为三类。即无弯钩的卷曲纤维,前弯钩纤维和后弯钩纤维。无弯钩的卷曲纤维,纤维的伸直过程较为简单,当它的前端与其他部分之间产生相对运动时,纤维即开始伸直。但是有弯钩的纤维,伸直过程较为复杂。通常将有弯钩纤维的较长部分称为“主体”,较短部分称为“弯钩”,位于牵伸前进方向的一端称为前端,另一端称为后端。弯钩与主体相连处称为弯曲点。弯钩的消除过程,即弯钩纤维的伸直过程,应看作是主体与弯钩产生相对运动的过程。主体和弯钩如果以相同速度运动,则不能将弯钩消除。 弯钩纤维能否伸直,必须具备以下三个条件:弯钩与主体部分必须有相对运动即速度差;伸直延续时间即速度差必须保持一定的时间;作用力即弯钩纤维所受到的引导力和控制力应相适应。 (二)纤维伸直过程的延续时间 纤维能否伸直以及伸直效果的好坏,在很大程度上取决于伸直过程的延续时间。对于后弯钩纤维,开始伸直的最大可能位置是主体部分的中点越过了快慢速纤维数量相等的R/点,如图5-3-14所示。事实上由于主体的长度较长,它的中点还未到达R/点时,其头端可能已经进入前钳口线FF/,由于前钳口的握持力迫使主体部分提前变速,因此延长了弯钩伸直的延续时间,提高了伸直效果;相反,对于前弯钩纤维,开始伸直的位置是弯钩的中点越过了R/点,而纤维弯曲点的位置还未到达前钳口,主体部分的中点尚未到达R/点。但当前弯钩纤维伸直发生后,由于弯曲点很快进入前钳口,迫使整根纤维作快速运动,使伸直过程提前结束,因此缩短了弯钩伸直的延续时间,降低了伸直效果。 可见,由于前钳口的强制握持作用,使后弯钩纤维伸直延续时间长,前弯钩纤维伸直延续时间短,所以,罗拉牵伸有利于后弯钩纤维的伸直。 (三)影响伸直平行效果的主要因素 实践证明,影响纤维伸直平行效果的主要因素有牵伸倍数及牵伸分配,牵伸型式,罗拉握持距和罗拉加压及工艺道数等。 1.牵伸倍数及牵伸分配 牵伸倍数的大小对于弯钩纤维的伸直效果有直接关系。弯钩纤维的伸直度可以用伸直系数η来表示。 η=主体部分的长度/纤维的实际长度 经过牵伸后,弯钩纤维的“主体”部分长度增大,“弯钩”部分长度减小,伸直系数相应增大。若用η表示伸直作用开始前的伸直系数,η/表示伸直作用结束后的伸直系数,则η/>η。 各种牵伸倍数下前弯钩纤维的伸直效果,可以用函数图像来表示,如图5-3-15所示。横坐标表示牵伸倍数,纵坐标表示伸直系数η/,各条曲线表示各种原始伸直系数的纤维在不同牵伸倍数下的伸直效果。图像共分为三个区。第①区表明牵伸倍数较小(E<3)时,伸直效果随牵伸倍数的增大而提高;第②区表示牵伸倍数增大(E>3)时,伸直效果先增后减,总的伸直效果不明显;第③区表示牵伸倍数更大(E>4~6)时,各线段趋于水平,即η/=η,无伸直效果。
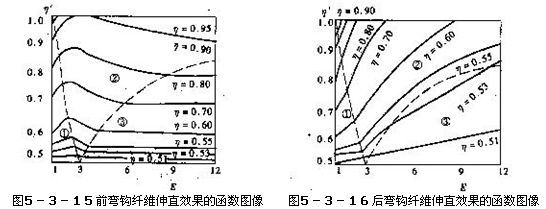
各种牵伸倍数下后弯钩纤维的伸直效果,也可以用函数图像表示,如图5-3-16所示。图中①、②、③三个区域的图像表明各种原始伸直系数的后弯钩纤维,经牵伸后,其伸直系数都随牵伸倍数的增大而提高。即牵伸倍数越大,后弯钩纤维的伸直效果越好。 从以上的分析可见,牵伸对伸直后弯钩有利,且牵伸倍数越大,对后弯钩纤维的伸直效果越好;而对于伸直前弯钩,伸直效果仅在牵伸倍数较小E<3时,才有一定的伸直作用。 由于梳棉生条中大部分纤维呈后弯钩状态,条子从条筒中引出后每经过一道工序,纤维发生一次倒向,所以使喂入头道并条机的生条中前弯钩纤维居多,喂入二道并条机的半熟条中后弯钩纤维居多。因此,在头道并条的后牵伸区采用较小的牵伸倍数(1.06~2.00),有利于前弯钩伸直;在二道并条的主牵伸区采用较大的牵伸倍数,有利于后弯钩的伸直。并条机道数间的牵伸配置采用头道小二道大,有利于消除后弯钩,可提高纤维的伸直度。 2.牵伸型式 不同的牵伸型式,其牵伸区具有不同的摩擦力界分布,对须条牵伸能力和弯钩伸直作用不同。曲线牵伸和压力棒牵伸,由于加强了牵伸区后部的摩擦力界,对纤维的控制力加强,且主牵伸区牵伸倍数增大,对纤维伸直作用较好。 3.工艺道数 由于细纱机是伸直纤维的最后一道工序,且牵伸倍数最大,有利于消除后弯钩,因此为了使喂入细纱机的粗纱中后弯钩纤维为主,在普梳纺纱工艺中,梳棉与细纱之间的工艺道数应符合“奇数原则”,这样有利于弯钩伸直。
|