内容提要:
在2007幕尼黑ITMA上展出的新型浆纱机几乎都带有浆前预加湿技术,这是一项当代浆纱工程中的新技术,自1999年巴黎展览会上美国西点公司、德国祖克、米勒、哈科巴公司、贝宁格公司等分别展出了新型浆纱机以来,浆前预加湿技术又有新的发展。经纱上浆前,经过预加湿处理,可使经纱强力提高,耐磨度提高,毛羽减少,从而提高了经纱质量及织造效率,也节约了一定的浆料。美国西点公司、德国祖克—米勒—哈科巴,卡尔。玛耶耳公司及贝宁格公司等公司先后生产出带有预加湿处理技术的新型浆纱机,使浆纱技术大大提高一步。我国郑纺机开发生产的有浆前预加湿技术的GA309 浆纱机已投放市场并通过国家级产品技术鉴定及验收,受到用户的好评。国家级产品技术鉴定及验收的专家们一致认为我国郑纺机开发生产的有浆前预加湿技术的GA309 浆纱机已达到世界先进水平。
关键词:浆前予加湿,减少毛羽,提高经纱强力,耐磨度提高织机效率,节约浆料。
浆纱工程是提高织机效率及织物质量的关键,而经纱的上浆率及上浆质量则是浆纱工程的重要考核内容。目前国内外在浆料配比上大都以变性淀粉,PVA浆料及丙烯酸三大浆料为主,世界年耗用各种浆料60万吨以上,其中PVA浆料约占6万吨,由于PVA污染环境已被列入淘汰的浆料。因此要发展高、中、低粘度和浓度的变性淀粉配以一定数量的丙烯酸取代PVA,一方面取消和降低PVA用量,另一方面因变性淀粉配用量的增加而降低成本,我国近年来历届全国浆料会议上明确提出不用或少用PVA浆料的要求。
国内外对如何进一步降低浆纱用量、提高上浆质量做过许多研究,特别对浆纱工艺技术研究取得重大进步,如远红外线辐射浆溶剂上浆、泡沫上浆及高压上浆技术等都不同程度 的提高了经纱质量、降低浆料用量、实现节能。1999年巴黎展览会上美国西点公司、德国祖克、米勒、哈科巴公司、贝宁格公司等分别展出了新型浆纱机,这种新型浆纱机采用经纱进入浆槽前进行预加湿处理技术,显示出了许多优点如经纱增强、耐磨、毛羽少,最显著的优点是比传统浆纱机节约浆料1/3,引起与会者重视。21世纪以来浆前预加湿技术又有了新的发展,不仅技术水平不断提高,而且应用面不断的增加。在2007幕尼黑ITMA上展出的新型浆纱机几乎都带有浆前预加湿技术。
1、国外浆纱浆前预加湿技术的设计:
经纱在进入浆槽前要先经过有一定温度的热水槽〔水温90°左右〕进行浸泡轧压,洗涤,去除经纱的短绒、灰尘、杂质、棉蜡及气泡等,提高经纱对浆液的亲附能力和吸收效果。如图1:经纱在热水槽中浸轧后即进入浆槽。
值得注意的是经纱片纱由热水槽引出时虽然已经压轧挤压,但仍带有一定水份进入浆槽中使浆液浓度逐步降低、水槽中水位降低。在设计时为了控制浆槽中浆液浓度,增加了浆液浓度自动监控系统,监控水槽的水温及水位高度的自动监控系统。使贮浆桶中浆液浓度始终以高于设计浓度的0.5%供给浆槽,显示了浆纱前预加湿技术的优点,使浆纱前预加湿技术与浆纱技术得到完美的结合。
浆液浓度及预加湿自动监控系统如图2,同时还要对热水槽中的水量及水的温度进行自动监控,实现了浆槽浓度与水槽温度、水位高度的监控的完美结合,从而控制浆槽中含固量稳定一致,使浆槽浆液浓度稳定一致及预加湿量稳定一致。:
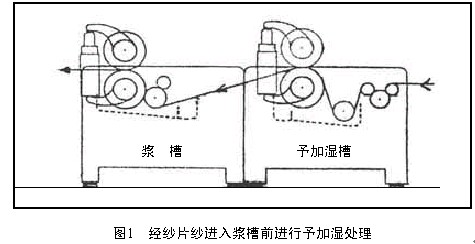
图2:浆液浓度及加湿量的自动监控系统〔为浆液浓度监控器〕〔图中为双浆槽式浆纱机〕
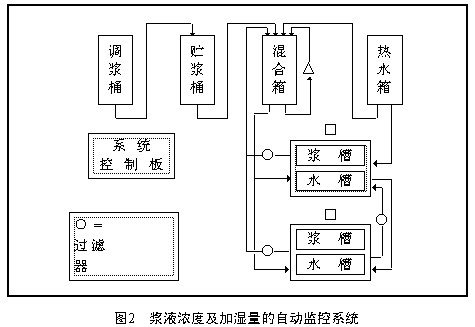
2、贝宁格浆前预加湿技术——预加湿及上浆联合机构
浆前预加湿技术可使浆纱质量稳定与提高并节省浆料。贝宁格浆前预加湿部分与上浆部分合在一起形成一个体系,整个系统是自动控制的。纱线喂入后经预加湿及上浆的全过程分四个部分如图3所示:
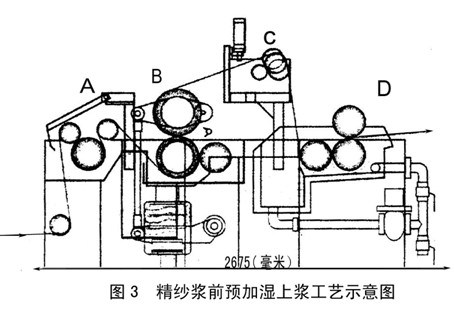
图3中:经纱经过A、B、C、D四个部分,占用全部经纱长度4367毫米。
A、经纱喂入部分:经纱在进入预加湿槽之前先经过喂入部分被回转的喂入罗拉握持并以一定的速度喂入到预加湿槽中。
B、经纱预加湿槽部分:经纱进入预加湿槽中受到一定温度的热水浸渍洗涤,最后经过较高压力的轧辊罗拉轧压,压出大部分水,轧后会有一定水份的经纱进入浆槽,达到节约上浆的目的。
C、经纱在上浆槽部分:经纱在浆槽中上浆并受到设定的较高压力的轧压,轧去多余的浆料并使经纱有一定的上浆率。
从经纱进入喂入部分到从浆槽中引出为止,全部经纱需要4.367米,喂入部分到浆槽出纱侧的水平距离为2.675米。
3、浆液浓度的自动控制:
由于经纱在预加湿槽中吸收的水份经轧压后仍带着一定的水份时入浆槽,因此使浆槽中浆液浓度逐步稀释降低。在新开车时经纱以1000~2000米/分的速度进入浆槽时浆液浓度不会降到设定浓度以下,因为起始上浆时浆槽浓度高〔如图4所示〕:
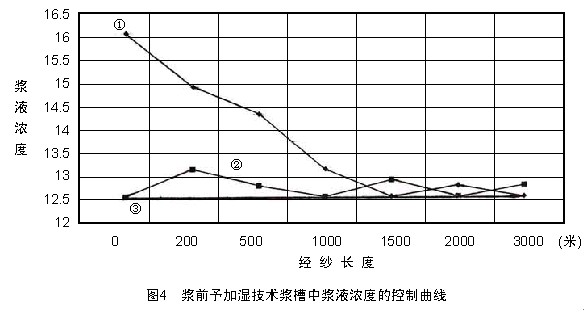
图4中:
①浆纱机新开车时浆槽中浆料浓度变化曲线;②正常运转中浆槽内浆料浓度自动控制曲线;
③设定的浆槽最低浓度线。
浆液浓度开始时为16.5%,但超过2000米后浆液浓度可能会低于设定浓度。为保证浆液浓度稳定不出现低于设定浓度的情况,在浆槽中设置了浆液浓度传感器自动控制浆液浓度,当浆液浓度接近设计浓度最低值时,传感器经过电子计算机通知贮浆桶自动向浆槽补充浓度较高的浆液,如此循环控制使浆液浓度基本稳定不会出现低浓现象。
图4为浆液浓度控制曲线,曲线③为设立的最低浆液浓度值,低于这个曲线的浆液浓度会影响上浆率。曲线②为正常生产中受传感器控制,浆液浓度则于不断自动补充较浓的浆料,使浆槽中浆液浓度不会出现低于设定的浓度最低值。曲线①为新开车时由于浆槽中浆液浓度较高,预加湿后的经纱经过1000~2000米后浆液浓度会接近设定的最低值,传感器开始工作,通过储贮浆桶自动补充浓浆液过程即进入曲线②的自动控制浆液浓度的状态
4、国外浆前预加湿技术具有以下优点:
4.1、美国西点公司在813型预加湿技术的浆纱机上经过各种对比试验发现不论经过加预加湿后吸水多少都会使经纱上浆率减少、毛羽减少、织机效率提高.一般预加湿后可使上浆率减少1/3,不仅节约生产费用并能提高织造性能。 4.2、经纱强力提高15-20%;4.3、经纱毛羽减少50%;4.4、提高经纱抗摩擦性能60%;4.5、降低经纬纱断头; 4.6、增加经轴的经纱长度;4.7、不需要对经纱再加湿;4.8、减少浆纱排出物的处理费用;4.9、改进经纱对浆料的附着力。
这些优点的核心是在上浆率降低1/3的前提下提高了浆后经纱性能、织机效率及产品质量。例如:
以国内某厂生产4545涤棉布为例,正常耗用浆料成本0.21元/米,若年产1000万米细布,全年可节约70万元。(预加湿技术可使每米布节约浆料0。07元)
山东德棉股份有限公司曾对于预加湿上浆技术在Karmayer浆纱机上进行了试验,试验品种为纯棉精梳14.6×14.6×382×283×165试验结果认为经过预加湿处理后提高了经纱强力,并保持一定的弹性,毛羽服贴较好,浆膜完整性好,提高了经纱耐磨性,织机效率提高2%左右,该厂全年浆料耗资1000万元左右,若全部应用预加湿技术,全年可节约成本200万元左右。上两例仅以节约浆料一项
进行对比,其它还可减少浆纱废液处理退浆费用,提高织机效率及产品质量等 。由于预加湿技术使经纱上浆率明显降低,给企业带来明显的经济效益。
5、贝宁格的浆前预加湿技术已在欧洲许多国家、地区应用并取得很好的效果。如:
5.1、德国某厂在生产纯棉织物时加工16-34公支(10-21英支)经纱进行浆前预加湿,上浆率在5-11%可节约浆料30-50%,节约浆纱费用30-40%。
在多尼尔喷气织机上织布时,织机速度为800-900转/分,10万纬断头停台数明显减少。
5.2、法国一工厂把浆前预加湿技术用于加工纯棉经纱约节约浆料20%,在苏尔寿片梭织机和哔加诺喷气织机都在使用浆前预加湿经纱后生产稳定。但M8300多相织机存在一定问题,断头增加,尚需改进。
5.3、法国Hacot纺织厂用浆前预加湿技术加工30-36英支精梳纱织布可节省浆料25%,但如果车速太快会使经纱在预加湿槽中经过时间减少35%,会使预加湿上浆出现问题,上浆不足。
5.4、意大利Fessivul纺织厂用浆前预加湿技术加工6-34英支经纱,可节省浆料35%,织机运行与不加湿的织机效率相同。
5.5、长丝预加湿在意大利Albini纺织厂也有应用,实践证明细度在50-60英支〔9000-12000旦〕的染色长丝纱经过预加湿处理可节约浆料20%,织机生产情况与不加湿的经纱情况基本相同。在生产100%丝纱中好的情况可节约30-40%的浆料。
由于加工长丝纱经过预加湿后有较多水份进入浆槽使浆液浓度降低,因此必须加大补充浆液浓度以使上浆稳定。
5.6、国外一些有关机构像德国邓肯道夫纺织工艺研究所会同织造厂、浆料厂及纺织院校进行了许多有成效的研究,认为:预加湿技术应根据产品品种、浆料、浆液浓度、粘度、压轧力、浆液温度及浆纱速度进行合理选配与调节,预加湿工艺中的压水力和水温应越高越好;必须及时检测浆液浓度,以免浆液浓度被带水的经纱稀释;预加湿的目的不仅是为了减少用浆量,更重要的是提高经纱质量及提高织机效率。
邓 肯 道 夫 预 加 湿 上 浆 试 验 报 告
表