1 各项主要工艺技术指标的相应关系
(1)精梳落棉率的多少与整个生产质量的关系极大,对精梳条结构(纤维伸直度、平行度、短绒含量、纤维单根化程度即纤维分离度、棉结杂质及纤维损伤状态)特别是对降低棉结杂质和条干CV值关系很大,还影响到合理用棉与降低成本。
(2)精梳条重量不匀率的大小关系到条干CV值的水平,它还与精梳前部工序的生条重量不匀率和精梳准备工序的重量不匀率有关,还影响到后工序的重量不匀率。
(3)精梳条棉结杂质的多少直接影响到半成品质量及成纱质量,它与生条含杂和原料、配棉情况、开清棉工艺流程、清棉、梳棉机械状态及工艺等关系密切,对精梳机构的梳理状态(锡林、顶梳与毛刷等)和吸风机构以及给棉形式等有关。
(4)精梳条条干CV值的大小密切关系到整个生产过程中的质量,它与准备工序和总牵伸倍数、后区牵伸分配、定量、罗拉隔距等工艺配置均有关。
(5)精梳条含短绒率的多少关系到成纱质量,它与原料、清梳工序以及精梳准备工序的短绒控制情况有关,也与梳理状态有关。它不但影响到成纱质量,而且还影响到棉结杂质的降低。
(6)精梳落棉含短绒率的多少与精梳条含短绒率的多少是呈反比例的,它关系到节约用棉和精梳机去除棉结杂质的性能。
以上六个方面的关系是互相关联和互相影响的,故也称之为综合性的工艺技术指标。为了完成上述各项工艺技术指标,必须对有关工艺进行具体的调整或微调,才能取得良好的质量效果。
2 各项主要工艺技术指标的应用原则与要求
2.1 精梳落棉率的应用原则与要求
(1)精梳落棉率与所纺纱号、纤维长度及短纤维排除率的关系?
精梳落棉率的多少是以所纺纱号与纤维长度为依据的,其关系见表1。精梳落棉率的多少对排除落棉中16 mm以下短绒率的影响很大,因为精梳纱的质量主要与落棉率的掌握程度有关,取决于去除短纤维后残留在纱内短纤维含量的多少。其关系与要求如表2所列。
表1 精梳落棉率与所纺纱号、纤维长度的关系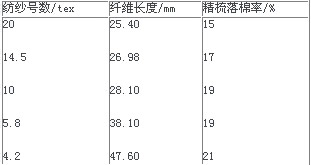
表2 精梳落棉率与短纤维的排除率 单位:%
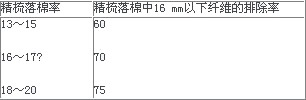
从表2可知,适当加大落棉率,对排除落棉中的短纤维是有利的,当然落棉中短纤维排除得越多,棉结杂质也随之减少。
(2)精梳落棉率的掌握
加工长纤维比加工短纤维的落棉率要多,一般速度可采用中速与中高速。精梳喂给量的变化对落棉率增减产生影响,喂给量增大则落棉率也增大,呈正比关系;反之喂给量减少,则落棉率也相应减少。如纺某一品种,纤维长度为40 mm,分离距离(即落棉隔距)在15 mm时,喂给量分别为4.9 mm与5.2 mm时,则落棉率P为:

(3)落棉率的调节
新型棉精梳机的落棉隔距(即分离距离)总共可调范围为6 mm。最近距离(在落棉刻度5处)位于钳板与分离罗拉距离为16 mm处,此时精梳落棉最少。最远距离(在落棉刻度11处)位于钳板与分离罗拉距离为22 mm处,此时精梳落棉最多。下面通过计算来说明分离距离与落棉率的关系。如纺某一产品,纤维长度为40 mm,喂给量为5.6 mm,分离距离(即落棉隔距)分别为15 mm和17 mm,则落棉率P为:

从以上可知,分离距离(即落棉隔距)改变1 mm,则落棉率可改变2%~2.5%。在变动落棉刻度时,必须重新检查与调整顶梳隔距,以免与钳板、胶辊等部件发生碰撞。除用上述变动方法调整落棉率外,尚有许多办法用以调节。切忌一味用改变落棉隔距的办法,这样会造成喂给部分产生问题,如喂给部分齿轮磨损与喂给不良等。可用下列办法调节:
①给棉罗拉棘轮改变1齿,落棉率可改变0.5%~1%;
②给棉形式改变,落棉率可改变4%~6%;
③锡林针齿改稀或加密,落棉率可改变1.5%~2%;
④顶梳梳针插入深度改变一档(共分5档,每档0.5 mm),落棉率可改变2%。
关于采用前进给棉与后退给棉,与品种、纤维性能长度有关。采用前进给棉时,一般落棉率掌握在5%~17%的范围内;采用后退给棉时,一般落棉率掌握在18%~25%的范围内。
2.2 精梳条重量不匀率的掌握与要求
精梳条重量不匀率影响到精梳条条干不匀和成纱的条干不匀以及重量偏差的稳定,对质量指标的评定均有影响。重量不匀率增大后,重量偏差控制也较困难。实践证明,棉卷、生条、精梳条、熟条以及粗纱的重量不匀都会造成成纱的重量不匀和重量偏差。当梳棉生条重量不匀率控制在2%~2.5%以下、精梳条重量不匀率控制在1%以下、并条熟条重量不匀率控制在0.8%以下、粗纱重量不匀率控制在0.9%以下时,细纱成纱的重量不匀率就能达到1.2%左右。
精梳条重量不匀率的掌握与要求如下:
①定期测试精梳落棉率,及时对眼差、台差进行控制(台差<±1%。眼差<±2%);
②统一工艺,做到同品种同机型一致,各部隔距、齿轮与锡林、顶梳型号规格一致,完整无缺齿;
③严格运转操作规程,防止换卷与接头时的接头不良;
④定时做好平揩车工作,确保机械状态良好;
⑤控制好车间的温湿度,防止粘卷、棉网破边或破洞等;
⑥按时清刷顶梳与锡林,定期校正毛刷对锡林的插入深度,也可适当加强毛刷清洁时间,以提高锡林的梳理效果。
2.3 精梳条条干CV值的掌握与要求
精梳工程任务之一为进一步分离纤维,促使精梳条中纤维完全单根化,提高纤维的伸直平行度,有利于成纱过程中牵伸装置对纤维运动的控制。对精梳工序的要求是:提高纤维的伸直度,由生条的50%提高到85%~95%。目前精梳条干CV值达到4.1%及以下时,即为达到乌斯特89公报的25%以内水平。
关于改善精梳条CV值的有效办法有下列几点:
①改善半制品结构。半制品结构包括纤维分离度、纤维伸直度、平行度及短纤维含量和棉结杂质的粒数。在纤维伸直过程中,纤维弯钩对纤维运动作用的影响很大,从梳棉至精梳之间要强调工艺的偶数配置,以合理改变弯钩方向。要减少棉条中的小棉束和棉结杂质,使纤维运动正常化,以改善条干水平;
②精梳条定量与乌斯特条干CV值关系很大,一般在机械状态良好的情况下,只需将精梳条干定量提高到20 g/5 m以上时,可使乌斯特条干CV值保持在4.0%或以下;
③解决由牵伸波、机械波与搭接波所造成的影响乌斯特条干CV值问题。牵伸波大多由牵伸机构不良、摩擦力界分布不合理造成,因牵伸装置对不同长度的纤维控制效果不同,牵伸波平均波长为纤维平均长度的2.5倍~3倍。新型精梳机一般经验为:高档精梳纱总牵伸14倍~15倍即可;中高档精梳纱11倍~12倍即可;一般精梳纱10倍以下即可。
机械波是由机械状态不良造成,主要原因有胶辊或罗拉偏心、弯曲或表面有轧伤或凹陷,以及胶辊壳与芯间隙大、轴承内花衣充塞、牵伸齿轮齿顶磨损、齿轮孔与轴或键槽配合公差过大、传动带不良。解决了这些周期性的不良影响,机械波即行消除。
搭头刻度对分离罗拉顺转开始时的分离接合起调节作用。如搭头长度不当,会在分离接合处出现接合波。这要在大车头内调整微调刻度(范围为-2~+1)即可解决,最好时乌斯特CV值可降低0.6个百分点及以下。
此外,如准备工序的并合根数与牵伸比的配置、准备工序棉卷重不匀率的控制以及胶辊与加压机构的状态改善、还有车间温湿度的合理控制等也都影响到精梳条乌斯特条干CV值的水平。
2.4 减少精梳条棉结杂质的措施
精梳另一主要任务即进一步清除生条纤维中残留的棉结杂质,以提高纤维的光洁度。通过精梳工序后,可清除生条中残留的棉结17%左右、杂质54%左右、短绒42%~48%。
减少精梳条棉结杂质的办法与要求如下:
①严格控制梳棉生条的短绒率(根据经验数据,由梳棉短绒率造成的棉结约占61%);
②加强车间温湿度的管理,减少粘卷等现象(相对湿度以57%~60%为宜);
③应根据所纺品种与纤维长度来选配金属锯齿整体锡林(齿面圆心角为90°与112°,齿条有四分割式与五分割式);
④合理调整毛刷定期清刷锡林的时间;
⑤根据纤维长度调节锡林定位;
⑥调整毛刷插入锡林深度;
⑦合理调节喂给量(包括给棉形式);
⑧检查与调节钳板闭合定时;
⑨检查与调整锡林的梳理隔距;
⑩合理调节顶梳插入深度,并选好胶辊以控制纤维,防止破边与缠花。
2.5 降低精梳条含短绒率的措施
我国有关标准规定16 mm以下长度的纤维为短纤维。生产实践证明:中号纱原料中12.7 mm以下短纤维含量每增加3%,则成纱CV值增加1%;细号纱原料中10 mm