1、 我国精梳机的现状
我国精梳设备经过近40年的发展,取得了巨大成就。截止到2000年,我国精梳机的台数己达到13264台,是1990年精梳机台数(为7081台)的1.87倍;自1990年到2000年每年平均增加103套(每套按6台计算),精梳机的万锭配台由原来的1.8台增加到3.9台,1998年精梳纱所占比例为15.1%,到2000年增加到19%。精梳机的速度己由原来A201A型的116钳次/min提高到FA266型的350钳次/min,精梳机的产量提高了3倍。精梳机的综合质量水平(如精梳条质量、精梳落棉质量及机器的稳定性等)及自动化水平有很大提高。
总之,我国精梳机技术水平及设备加工制造水平与世界先进水平的差距正在缩小。目前,我国精梳机的机型繁多、品种不一,精梳机的速度水平与纺纱质量水平差别很大;按精梳机的工艺速度可化分为四个层次:第一层次是工艺速度在300钳次/min以上的高效能精梳机,如FA266型、F1268型及PX2-J型精梳机;第二层次是工艺速度在200钳次/min~280钳次/min的精梳机,如FA261型等;第三层次是工艺速度在160钳次/min/~190钳次/min的精梳机,如FA251型等;第四层次是工艺速度在120钳次/min~155钳次/min的精梳机,如A201B、C、D型。在这四个层次中,以A201系列精梳机最多,约为7200台[2>,该机速度低、纺纱质量差。因此在积极推广应用高效能精梳机的同时,利用精梳新技术对不同层次的精梳机进行技术改造,使精梳设备的整体技术水平和纺纱质量全面提高,为改善我国棉纱的产品结构、提高产品档次和产品竞争力奠定技术基础。
2 高效能精梳机的推广应用
采用高效能精梳机的经济与技术优势如下:
(1)高效能精梳机速度高、产量高,万锭配台、用人及占地面积少。
精梳机产量与精梳机的速度、小卷定量、给棉长度及每台精梳机的眼数成正比。用公式表示为:
G=60×A×g×n×a×(1一c%)/10002 ①
式中:
A——给棉罗拉的给棉长度(mm);
g——精梳小卷定量(g/mm);
n——精梳机的速度(r/min);
a——每台精梳机的眼数;
c——精梳机的落棉率(%)。
由①式算得FA266型、F1268型与A201D型精梳机产量见表1。
表1 精梳机的产量比较
由表1可知:在精梳机的给棉长度与精梳落棉率相同的情况下,FA266型、F1268型精梳机的产量为A201D型精梳机产量的4.15倍。
纺14.5 tex及18.2 tex精梳纱精梳机的万锭配台数见表2。
表2 精梳机的万锭配台数量
由此可知:FA266型、F1268型精梳机的万锭配台数只有A20lD型精梳机的l/4;占地面积和用人也只有A20lD型精梳机的l/4;万锭精梳机耗电量大大减少。因此采用高效能精梳机具有的巨大的经济效益。
(2)高效能精梳机的机械性能与纺纱质量水平高。由于高效能精梳的分离罗拉传动机构、钳板传动机构及钳板组件等关键机构设计合理,机器长时间运转时,故障少、坏车少、稳定性好。精梳条的质量指标(如条干CV值、重量不匀率、精梳条含短绒率等)及精梳落棉指标(精梳落棉率、落棉含短绒率等)都能达到规定要求。
(3)高效能精梳机自动化水平高,劳动强度低。
在高效能精梳机上普遍采用了高灵敏度的自停装置、计算机监控系统、PLC程序控制系统等 3 A201系列精梳机的技术改造
3.1 A201B(C、D)型精梳机存在的问题
3.1.1 整体基础差
A201B型、C型精梳机车头、机中、车尾及圈条器整体紧固作用差,特别是车尾和圈条器之间仅用两根撑杆连接,缺乏牢固性;高速时机器振动加剧。另外在车头内传动分离罗拉的差动齿轮、分离齿轮及传动钳板机构的滑杆、滑块等主要机件的润滑条件差,机器高速时机件的磨损大、损坏多。
3.1.2 承卷罗拉惯性大、给棉量难以控制由于A201系列精梳机的承卷罗拉为间歇转动,承卷罗拉与精梳小卷的惯性力随车速的提高而急剧增加,因此机器的振动和噪声增大,且承卷罗拉每次的给棉量难以控制。
3.1.3 纺纱适应性差
由于A201系列精梳机只有前进给棉,棉丛的梳理效果与精梳落棉量受到限制,难以适应纺高档精梳纱的要求。
3.1.4 钳板组件的重量大
A201系列精梳机钳板机构复杂,有上给棉罗拉、下给棉罗拉、给棉棘轮、上钳板座、下钳板座、上摇架及上下钳板等组成;且机件的材料是铸铁与钢,比重大,整个钳板组件重量为16.2 kg[3>。因此精梳机高速时,钳板组件的惯性力和冲击力大,机器的振动和噪声很高。
3.1.5 钳板钳唇结构设计不合理
A201系列精梳机钳板钳唇结构存在以下两个问题:一是钳板钳口对棉层的握持状态是一点(或称单线)握持,当精梳小卷的定量较小时,易形成对棉层的横向握持不匀,在锡林梳理时出现“抽筋拔皮”现象,造成棉网破洞与破边;且速度越高,“抽筋拔皮”的现象越严重。二是钳板钳口的“死隙”长度较长,约为7.43 mm[4>;从而使钳板钳口外棉丛的受梳长度减短,影响锡林对棉丛的梳理效果。
3.1.6 梳理隔距大、梳理效果差
由于A201系列精梳机钳板摆动的支点在锡林轴心的下方(称为下支点式钳板摆动机构),与中支点式(即钳板摆动支点与锡林轴同心)及上支点钳板摆动机构相比,梳理隔距的极差值与变异系数都大;因此梳理效果差。A201C型、FA251型及FA261型精梳机梳理过程中的隔距变化情况见表3[5,6,7>;梳理隔距的极差值与变异系数见表4。
表3 梳理隔距的变化情况
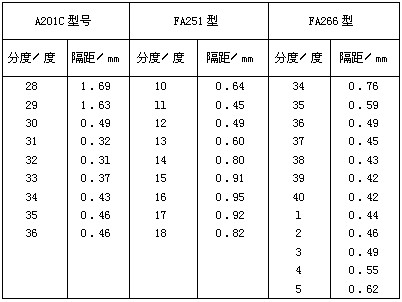
注:A201C型及FA251型精梳机最紧点隔距为0.3mm;FA266型精梳机为0.4 mm。
表4 梳理隔距的极差值与变异系数
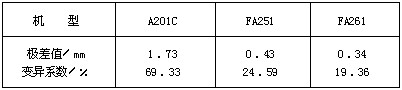
3.1.7 分离罗拉传动机构冲击大、工艺性能差<BR>A20lB(C、D)型精梳机分离罗拉传动机构是采用内差动轮系,此种传动方式存在的问题是:
(1)由于分离齿轮和差动齿轮采用少齿差传动,且内、外齿轮的转动惯量大,高速时齿轮的冲击力大、噪音高、传动平稳性差,机件易损坏;
(2)工艺性能差,如分离罗拉的有效输出长度大、棉网的接合率低,高速时易出现棉网破洞与破边现象。
3.2 技术改造的目标
3.2.1 提高车速
提高车速、增加单机产量、提高劳动生产率、扩大精梳生产能力是A20l系列梳机技术改造的主要目标。经改造后,机器的工艺速度应达到160钳次/min~180钳次/min。
3.2.2 提高产品质量
在提高车速、增加产量的同时,使精梳条的条干CV值、重量不匀率、精梳条中的短绒含量、精梳落棉含短绒率等质量较改前有明显改善,为提高成纱质量创造条件。
3.2.3 扩大纺纱品种
能够适纺细号、特细号高档精梳纱;并能适纺细绒棉和长绒棉。
3.2.4 改善劳动环境
降低精梳机的噪声,改善工人的劳动条件和劳动环境。
3.3 技术改造的措施
90年代初期,上海一纺机、无锡纺机等单位对国产A201B型、C型精梳机进行了技术改造,其改造的主要内容是:
(1)车头部分采用整体油浴箱,以改善车头传动齿轮的润滑状态、增强车头的整体钢度;
(2)植针锡林改为整体锡林,以提高锡林的寿命与梳理效果;
(3)分离罗拉由内差动轮系改为外差动轮系,以减小差动齿轮的运动惯量;
(4)采用毛刷单独传动,以提高毛刷对锡林的清洁效果[8>。机器经改造后,工艺速度水平达到155钳次/min,纺纱质量水平也有所提高,达到了A201D型精梳机的水平。为了实现技术改造的目标,需对A201系列精梳机进行深层次的技术改造,建议改造内容如下。
3.3.1 采用承卷罗拉连续回转
采用承卷罗拉连续回转的优点是:
(1)可消除承卷罗拉间歇回转时的惯性力,并消除了由此产生的冲击和噪声;
(2)承卷罗拉的给棉量可得到有效的控制。
3.3.2 缩短短轴销偏心距
A201系列精梳机短轴销偏心距的大小对机器的高速性能及工艺性能都有较大影响:
(1)短轴销偏心距的减小,钳板摆轴的角位移、钳板的运动量、钳板的最大加速度值等将减小,其对应关系见表5[9>;由此可知,短轴销偏心距由70mm减为60 mm时,钳板摆轴的最大角加速度减小 22.48%,钳板的最大加速度值减小23.48%;因此减小短轴销偏心距是减轻机器振动、降低噪声及进一步提高车速的重要技术措施。
&nb